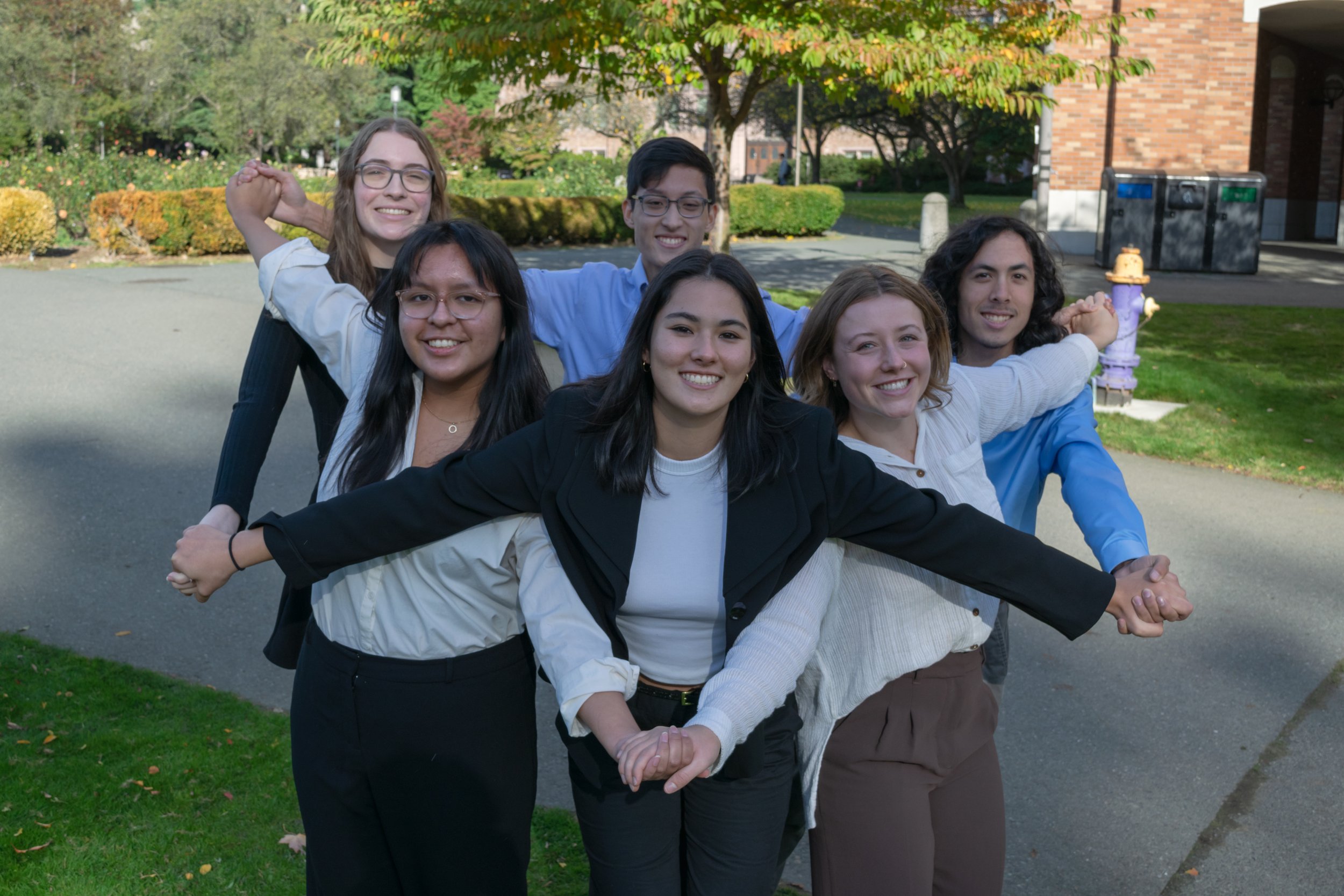
OUR SUBTEAMS
✦
OUR SUBTEAMS ✦
Building our robots requires investment from individuals who come from a wide range of disciplines. ARUW is split into sub-teams according to these key disciplines. The sections below outline the skill areas and projects that each sub-team is working on.
Note for applicants: we do not require that your major matches the focus area you choose to work on in our team. We strongly encourage you to apply to the sub-team(s) you are most interested in, regardless of your chosen academic degree.
ADMIN TEAM
Performs a wide range of tasks that help keep our club running smoothly, namely raising money for club expenses including operating costs, materials, travel & housing, and hosting events. Other tasks involve managing our business, outreach, and PR needs.
Key Projects:
Reaching out to companies and acquiring sponsorships.
Maintaining relationships with current sponsors.
Media production: photography, videography, editing, etc.
Running our social media accounts.
Maintaining our website.
Organizing community outreach events.
Mechanical Team
Designs our robots using computer-aided design (CAD), prototypes mechanisms, manufactures components, and assembles and wires the final robot.
CAD is done in SolidWorks, and manufacturing processes include 3D printers, mills, lathes, and more.
The mechanical subteam is split into squads of 4-7 people for each robot, with each squad being led by a veteran member.
Key projects:
Completing a robot from each squad.
Improving design and manufacturing processes.
SOFTWARE Team
Implements software systems for our main robot controllers, auto-aiming & auto-navigation capability, and electrical subsystems. Develops control loops for actuator control and designs neural networks for detection tasks. Spans embedded microcontrollers and desktop development. Additionally, we develop and maintain tooling platforms for model annotation/training and wireless real-time robot vision rendering.
Codebases are primarily written in C++, Python, and Rust for onboard robot systems. For our machine learning and detection models, we utilize PyTorch and TensorRT. Our full stack tooling platforms are hosted and developed in-house, with modern platform and web technologies.
Key projects:
Maintaining and expanding our open-source robot control systems library, Taproot.
Improving performance and accuracy of machine learning-based target classification & detection systems.
Refining localization, mapping, path planning, and autonomous navigation systems.
Designing full stack tooling platforms, including model annotation/training, vision rendering, and systems modeling.
Electrical Hardware Team
Designs complex power and signal systems for all types of robots, including innovative and custom Printed Circuit Board (PCB) designs, as well as meticulously crafted and organized wiring systems that ensure efficient and reliable operation.
PCB designs are done in Altium, with electrical simulations in LTspice and PLECS.
Key Projects:
Designing, building and testing a 2000 Joule-stored energy onboard capacitor bank, with embedded microcontroller, synchronous buck/boost controllers, dynamic software control.
Designing, building, and testing a brushless Electronic Speed Controller (ESC) with regenerative braking capabilities.
Designing power & signal multiplexers and distribution boards.